SLM
SLM (Selective Laser Melting) is a metal-based 3D printing process in which a laser is used to selectively melt fine metal powder layer by layer to create a solid component.
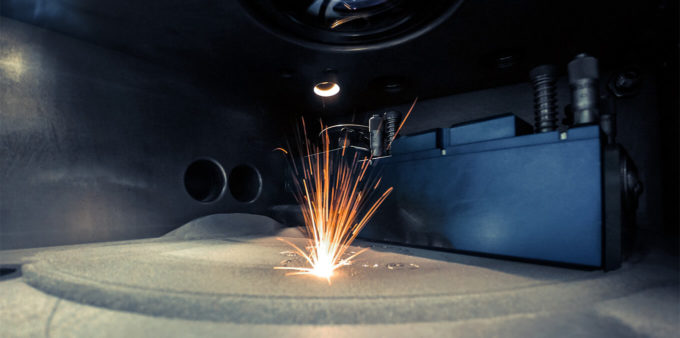
How it works
In the SLM process, a thin layer of metal powder is applied to a building platform system. A laser beam scans the areas relevant to the component and melts the powder completely (melt pool). The building platform then lowers by the thickness of one layer, and new powder is distributed. The process is repeated until the entire component is completed. Finally, the component is removed from the powder bed and, if necessary, reworked (e.g. removal of supporting structures, heat treatment, sintering).
Typical materials
- Stainless steel (e.g. 316L)
- Tool steels (e.g. H13)
- Aluminium alloys
- Titanium and nickel-based alloys
Fields of application
- Medical technology: manufacturing of patient-specific implants and prostheses.
- Aerospace: lightweight components with complex internal structures.
- Automotive industry: functional components, prototypes and tools (e.g. injection moulds).
- General mechanical engineering: individual parts in small quantities with special geometries.
Advantages and disadvantages
Advantages:
- High density and strength of the manufactured parts, comparable to conventionally manufactured metal components.
- Great design freedom (e.g. conformal cooling channels).
- No special moulds or milling tools required.
Disadvantages:
- High procurement and operating costs for equipment and powder.
- Limited installation space compared to conventional casting or milling techniques.
- Often requires post-processing (e.g. heat treatment for stress relief).