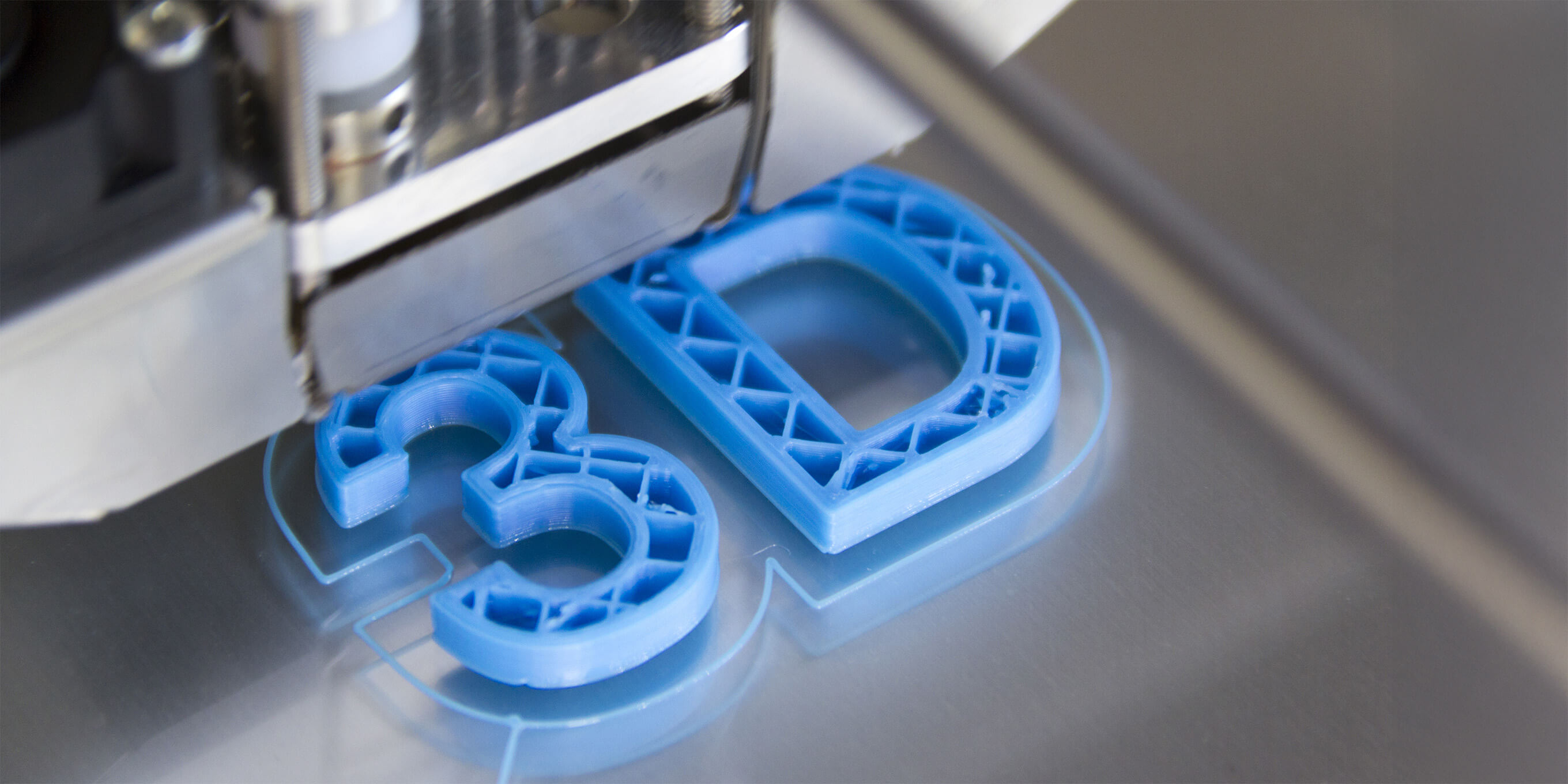
Customised products through 3D printing
published on 21. February 2025
Do you want to create your own design for your vehicle? But you can’t do it with standard components and a custom part is out of the question because the expected tool costs are not in line with the cost-benefit ratio?
3D printing is the answer! This production process offers new possibilities for anyone who needs smaller series but does not want to compromise on high-quality, precisely fitting components. The days when only huge quantities were profitable are over. Additive manufacturing takes your ideas to the next level:

High-quality production at high speed
– and low cost!
Classic die casting or injection moulding can quickly cost tens of thousands. With 3D printing, however, components can be produced much more cost-effectively and in a shorter time. That’s because not every component has to be cast: modern plastic 3D printing processes (e.g. FDM) now deliver parts that are suitable for everyday use and can be produced quickly and cost-effectively.
In the past, this technology was only used for prototyping, but now 3D printing is conquering series production. And for good reason. The quality of printed parts is often no longer distinguishable from cast parts. There is nothing to prevent them from being used as series parts in continuous operation.
Ideal solutions for small series
Since no elaborate casting moulds are required, design adjustments can be made quickly and, above all, cost-effectively. This manufacturing process offers unprecedented possibilities, especially for manufacturers of small series with a demand of a few hundred parts per year. No more capital tie-up, you only pay for what you really need. Take a look at the sample calculation!
Your advantage: No minimum order quantities, no expensive storage reserves. We produce exactly what you need, when you need it.
Your design has changed? No problem! Individual adjustments are possible at any time, without having to mill or cast new tools. You change the CAD, the printer implements it.
A calculation example
100 vehicles are to be built per year. Each vehicle requires a specially manufactured bracket to mount a worklight.
Injection moulding | 3D printing | |
---|---|---|
Tool costs: | 25,000.00 € | 0 € |
Unit cost: | 5.00 € | 45 € |
Tool costs per holder, amortised over 1 year: | 250,- € | 0 € |
Tool costs per holder, amortised over 2 years: | 125,- € | 0 € |
Tool costs per holder, amortised over 3 years: | 83.33 € | 0 € |
Parts price, 1 year: | 255,- € | €45 |
Parts price, 2 years: | €130 | €45 |
Parts price, 3 years: | €88.33 | €45 |
Custom parts are possible even with only 100 vehicles per year. While cast parts only start to pay off in large quantities, 3D printing makes an individual look affordable even for the smallest of series.
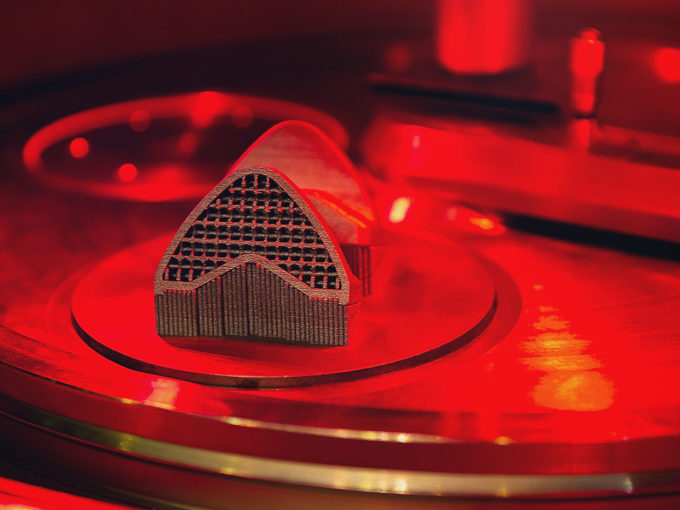
More than just plastic
3D printing is not limited to plastics. A lot has happened in the metal sector too: Thanks to metal 3D printing, high-strength components are being created that are ideal for special-purpose vehicle construction or other demanding applications.
This eliminates both the high tooling costs and the long delivery times associated with conventional casting processes – an advantage, especially if you only need a small number of parts.
Toolmaking in metal printing
Get the best of both worlds. Not only components themselves, but also casting moulds can now be efficiently produced using 3D printing. Particularly for smaller series, frequent design changes or complex geometries, the additive process offers real advantages over conventional milling processes.
Your advantages at a glance:
- High precision – even complex contours and undercuts can be easily realised
- Rapid customisation – design changes can be easily implemented without new milling
- Lower costs – lower initial investment and no capital tie-up due to large tool
This is how classic casting processes can be designed to be modern and flexible – and adapt to your pace.
Wettbewerbsvorsprung durch Schnelligkeit
In der heutigen Zeit ist es entscheidend, neue Ideen rasch auf den Markt zu bringen. 3D-Druck beschleunigt diesen Prozess enorm: Musterteile und Prototypen entstehen oft innerhalb von Stunden oder wenigen Tagen. So können Sie Ihre Entwicklungszyklen verkürzen und Ihre Teams gewinnen wertvolle Zeit für weitere Innovationen.
Dieses Plus an Agilität verschafft Ihnen einen deutlichen Wettbewerbsvorteil. Wer schneller liefern, früher testen und seine Produkte stetig verbessern kann, setzt sich in einem eng getakteten Marktumfeld klar durch. So bleiben Sie nicht nur vorne dabei, sondern sichern sich langfristig auch das Vertrauen Ihrer Kunden.
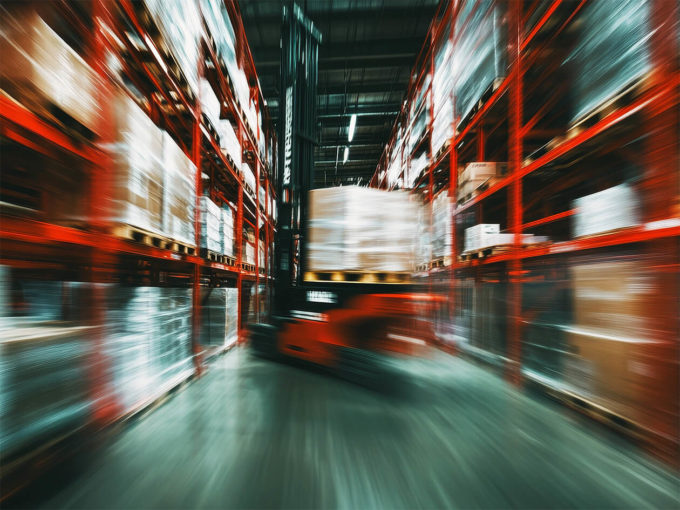
Fazit
3D-Druck räumt mit dem Vorurteil auf, dass Customteile immer teuer und zeitintensiv sein müssen. Ob Gehäuse aus Kunststoff, ein metallisches Endbauteil oder sogar eine neue Gussform für herkömmlichen Druckguss – die additive Fertigung macht es möglich. Gerade Fahrzeughersteller, die nur geringe Stückzahlen produzieren, profitieren dreifach: kürzere Lieferzeiten, weniger Kostenrisiko, schnell umsetzbares Design.
Haben Sie Fragen oder wünschen Sie eine persönliche Beratung? Kontaktieren Sie uns und lassen Sie sich zeigen, wie 3D-Druck Ihren Werkstatt- und Produktionsalltag revolutionieren kann.